Implants: A better fit through mathematics
Individuals with implants may soon be able to feel the benefit of basic scientific knowledge in their own bodies. This is one of the findings of a translational research project conducted by the Austrian Science Fund FWF. The project demonstrated how 3D models and special mathematical methods could be used to improve the design and integration of implants in the body on a patient-specific basis. Data was gathered from computer and magnetic resonance tomography and used to generate 3D models specifically for shoulder joints and their replacements. The data was analysed in a procedure known as the finite element method, and possible individual optimisations were calculated. The project exemplifies the acute benefit of research findings from the Translational Research Programme, which ended at the close of the first quarter of 2012.
This project brought together basic scientific knowledge from the areas of mathematics, medicine and computer science with the aim of optimising replacement shoulder joints individually (patient-specific). Headed by Dr. Karl Entacher from Salzburg University of Applied Sciences and Dr. Peter Schuller-Götzburg from the Paracelsus Medical University in Salzburg, the project initially computed human shoulder joint models and then used them as the basis for the analytical simulation of varying load conditions.
The team commenced by using imaging techniques to create the computer models. To this effect, computer tomography was used to build up images of human shoulder joints on a layer-by-layer basis. As Dr. Entacher explains: "Modern tomography techniques allow us to create images of an entire shoulder joint layer-by-layer, and the layer thicknesses that we can achieve today make excellent resolution possible. We were able to use this image data to create computer-generated 3D models of each patient´s individual shoulder joint, forming the basis for our subsequent analysis."
This subsequent analysis was based on a mathematical process called the finite element (FE) method. With this method, the objects to be analysed are depicted in small - but finite - elements. Their behaviour can then be computed numerically and simulated, taking into account variables such as material properties and load, as well as the limits of movement. In the process, it is possible to model the most varied conditions that the joint might face. Speaking about these conditions, Dr. Entacher comments: "Our aim was to simulate the implant at different positions and different angles in the body, as well as to simulate the anatomical make-up of different, individual patients." In fact, the model was so sophisticated that different types of tissue, such as soft tissue or different bone sections, could be selected. It was also possible to create virtual sections to move different parts of the bone or the implant to any given position. All in all, this enabled the scientists to gather valuable data for the patient-specific optimisation of shoulder and even tooth implants. This could provide future patients with important information on the positioning, the type or the performance of their implant before they have an operation.
Most read news
Organizations
Other news from the department science
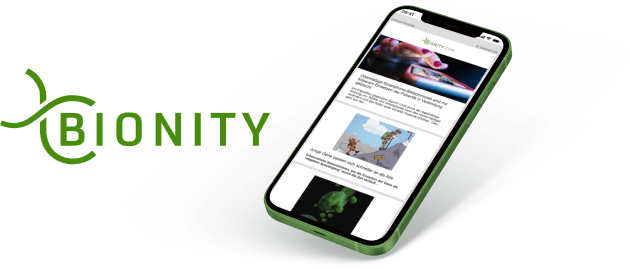
Get the life science industry in your inbox
By submitting this form you agree that LUMITOS AG will send you the newsletter(s) selected above by email. Your data will not be passed on to third parties. Your data will be stored and processed in accordance with our data protection regulations. LUMITOS may contact you by email for the purpose of advertising or market and opinion surveys. You can revoke your consent at any time without giving reasons to LUMITOS AG, Ernst-Augustin-Str. 2, 12489 Berlin, Germany or by e-mail at revoke@lumitos.com with effect for the future. In addition, each email contains a link to unsubscribe from the corresponding newsletter.